Die Suche nach verfügbaren Transportkapazitäten ist oft eine Herausforderung, insbesondere wenn die Nachfrage hoch ist. Die traurige Wahrheit ist jedoch, dass auch viel Kapazität verschwendet wird. Wir sehen dies beispielsweise an der Zahl der täglichen Leer-Backhauls. Es gibt jedoch noch eine andere Form der Kapazitätsverschwendung, die viele Verlader übersehen: Kapazitätsverschwendung aufgrund nicht optimierter Ladepläne. Vereinfacht ausgedrückt: Anhänger verlassen Anlagen, wenn sie nicht bis zu ihrer maximalen zulässigen Kapazität voll beladen sind.
Im Juni 2023 haben wir unsere Mitglieder befragt Indago Forschungsgemeinschaft für Lieferketten – allesamt Supply-Chain- und Logistik-Führungskräfte von Produktions-, Einzelhandels- und Vertriebsunternehmen – und fragten sie: „Wie sicher sind Sie, dass die LKWs, die Ihre Lager verlassen, bis zu ihrer maximalen zulässigen Kapazität beladen sind?“
Von den befragten Mitgliedern, die per LKW-Ladung versenden, gab fast ein Drittel (32 %) an, dass sie nur „ziemlich sicher“ (11 %) oder „überhaupt nicht sicher“ (21 %) sind, dass die LKWs, die ihre Lager verlassen, maximal beladen sind Rechtsfähigkeit – das heißt, dass sie die Produktmenge, die in einen Anhänger passt, unter Berücksichtigung von Platz, Gewicht, staatlichen Vorschriften und anderen Einschränkungen vollständig optimiert haben. Etwas mehr als ein Drittel (37 %) gab an, „sehr sicher“ (16 %) oder „sicher“ (21 %) zu sein.

Warum passiert das? Es gibt verschiedene Gründe, darunter auch diesen, der von einem Indago-Manager hervorgehoben wurde:
„Es ist der klassische Kompromiss zwischen Last und Zeit. Wenn die Ladung warten kann, beispielsweise bei haltbaren Konsumgütern, ist es einfacher, den gesamten Anhänger zu füllen. Wenn die Ladung jetzt bewegt werden muss, ist der Anhänger wahrscheinlich nicht voll.“
Ein weiterer Grund ist, dass viele Unternehmen keine Software zum Erstellen/Optimieren ihrer Lasten verwenden. Nur etwa ein Viertel der Befragten unserer Indago-Mitglieder (26 %) nutzen Software zum Erstellen/Optimieren ihrer Lasten; 43 % nutzen Excel oder machen es manuell.
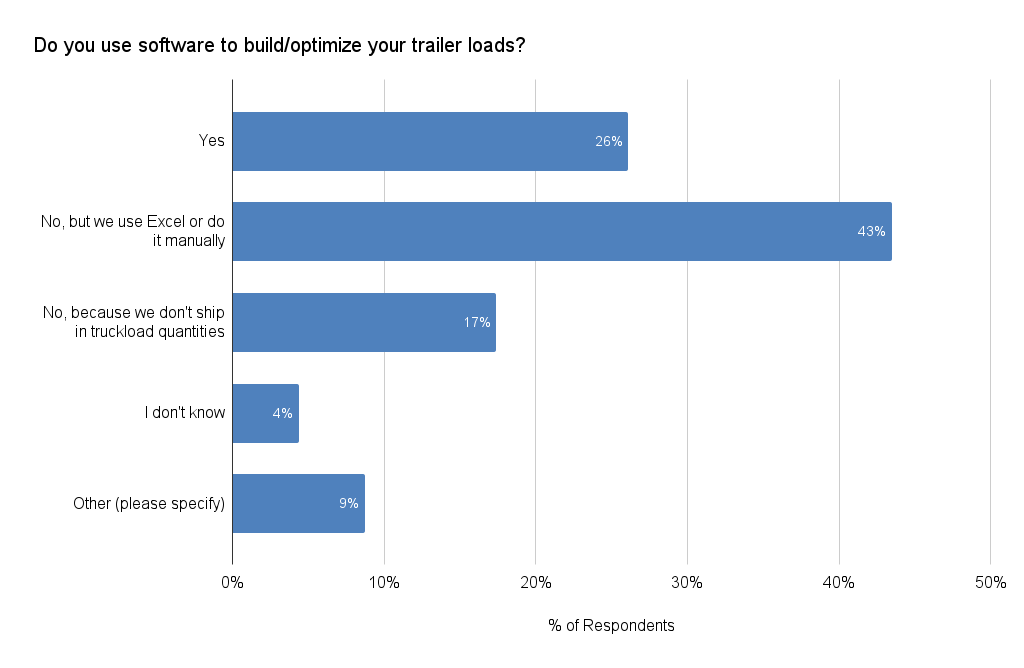
Welche Vorteile können Unternehmen durch die Bewältigung dieses Problems erzielen? Wie hilft Technologie?
Das sind die Schlüsselfragen, die wir in a besprochen haben aktuelle Talking Logistics-Folge mit Jennifer Phillips, Transportdirektorin bei Riviana Lebensmittel; Zachary Dale, Supply Chain Continuous Improvement Manager bei Riviana Foods; und Tom Moore, Partner bei Transport | Lageroptimierung (T|WO).
Riviana Foods-Fallstudie
Riviana Foods, eine hundertprozentige Tochtergesellschaft von Ebro-Lebensmittel (mit Hauptsitz in Madrid, Spanien) ist „Amerikas führendes Reisunternehmen und der umfangreichste Vermarkter von Wildreis weltweit.“ Das Unternehmen erzielte im Jahr 1 einen Umsatz von über 2022 Milliarde US-Dollar und verfügt über ein großes Werk in Memphis, TN, das im vergangenen Jahr über 10,500 Sendungen abwickelte, hauptsächlich per LKW-Ladung, Intermodalverkehr und Güterwagen.
Wie Jennifer in ihren Eröffnungskommentaren betonte, besteht die Komplexität ihrer Logistik- und Transportabläufe darin, dass „man alles bekommt, von Reisbechern, die sehr leicht und luftig sind, bis hin zu Kisten mit drei 20-Pfund-Säcken Reis darin.“ Daher haben wir ein breites Spektrum an Palettengewichten, Produkten, bei deren Stapelung man vorsichtig sein muss, und anderen Aspekten.“
Was war im Hinblick auf den Ladungsaufbau die geschäftliche Herausforderung oder Verbesserungsmöglichkeit, die Riviana angehen wollte? Im folgenden kurzen Clip teilt Jennifer einige der Herausforderungen mit, denen sie gegenüberstanden, darunter beschädigte Waren, viele Nacharbeiten im Vertriebszentrum und zurückgegebene Anhänger, weil sie die Achslastgrenzen überschritten hatten:
[Eingebetteten Inhalt]
Ein weiterer Treiber war die Nachhaltigkeit. „Wir verfolgen Nachhaltigkeit mit Ebro in Spanien“, sagte Jennier. „Ziel war es also nicht nur, die Anzahl der Ladungen zu reduzieren und Einsparungen bei Frachtkosten und Kosten pro Zentner zu erzielen, sondern auch, Emissionen zu reduzieren und auch Vorteile auf der Nachhaltigkeitsseite zu erzielen.“
Ich fragte Zach nach den wichtigsten Kennzahlen, die sie verbessern wollten. Neben der Nachhaltigkeit konzentrierten sie sich auf mehrere andere wichtige Kennzahlen und Ziele, darunter Frachtausgaben, Ladungsqualität, Umschlag und Schulung der Lader sowie Schadensreduzierung.
„Unsere Ladungsgewichte lagen überall und unter dem Industriestandard“, erklärte Zach, „aber das Ladungsaufbautool, das wir damals verwendeten, war nicht robust genug für das, was wir brauchten.“ Sehen Sie sich den kurzen Clip unten an, um mehr über die Tool-Einschränkungen zu erfahren, mit denen sie konfrontiert waren:
[Eingebetteten Inhalt]
„Eines der Probleme besteht darin, dass es sich um ein sehr komplexes Thema handelt“, fügte Tom hinzu. Im folgenden kurzen Clip erklärt er es weiter:
[Eingebetteten Inhalt]
„Es ist eine Sache, eine Ladung zu maximieren, eine andere, eine Ladung zu maximieren, zu zeigen, wie es gemacht werden kann, und sicherzustellen, dass es legal und schadensfrei ist, denn es hat keinen Wert, etwas zu versenden, das beschädigt werden kann“, sagt Tom.
Welche Faktoren veranlassten Riviana letztendlich dazu, mit T|WO zusammenzuarbeiten, als sie nach Technologielösungen suchten? Wie sind sie bei der Umsetzung der Lösung vorgegangen? Welche Ratschläge oder Empfehlungen würden sie anderen Unternehmen geben, die gerade erst am Anfang dieser Reise stehen?
Jennifer, Zach und Tom haben einige großartige Einblicke und Ratschläge zu diesen und weiteren Fragen gegeben, daher möchte ich Sie dazu ermutigen Sehen Sie sich die ganze Folge an für mehr Details. Spoiler-Alarm: „Der Go-Live verlief sehr gut“, sagte Zach. „Wir sahen fast augenblicklich eine Gewichtszunahme von 4 % pro Ladung. Der Return on Investment war sehr schnell – es dauerte Monate, nicht Jahre. Insgesamt konnten wir feststellen, dass sich unsere Kennzahlen sehr schnell verbesserten.“
- SEO-gestützte Content- und PR-Distribution. Holen Sie sich noch heute Verstärkung.
- PlatoData.Network Vertikale generative KI. Motiviere dich selbst. Hier zugreifen.
- PlatoAiStream. Web3-Intelligenz. Wissen verstärkt. Hier zugreifen.
- PlatoESG. Automobil / Elektrofahrzeuge, Kohlenstoff, CleanTech, Energie, Umwelt, Solar, Abfallwirtschaft. Hier zugreifen.
- PlatoHealth. Informationen zu Biotechnologie und klinischen Studien. Hier zugreifen.
- ChartPrime. Verbessern Sie Ihr Handelsspiel mit ChartPrime. Hier zugreifen.
- BlockOffsets. Modernisierung des Eigentums an Umweltkompensationen. Hier zugreifen.
- Quelle: https://talkinglogistics.com/2023/07/20/riviana-foods-using-optimized-load-building-to-reduce-transportation-costs-and-improve-sustainability/
- :Ist
- :nicht
- 1 Milliarden Dollar
- 10
- 2022
- 2023
- 500
- a
- Über Uns
- Buchhaltung
- Erreichen
- hinzugefügt
- Zusatz
- Adresse
- Adressierung
- Beratung
- Aufmerksam
- Alle
- ebenfalls
- Betrag
- an
- und
- Ein anderer
- SIND
- AS
- gefragt
- At
- verfügbar
- Taschen
- BE
- weil
- Sein
- unten
- Vorteile
- Milliarde
- breit
- Building
- Geschäft
- aber
- by
- CAN
- Kapazität
- vorsichtig
- Häuser
- Fälle
- Center
- sicher
- Kette
- challenges
- Herausforderungen
- klassisch
- Bemerkungen
- Unternehmen
- Unternehmen
- Komplex
- Komplexität
- Überlegungen
- Einschränkungen
- Verbraucher
- Inhalt
- kontinuierlich
- Kosten
- Kosten
- Organschäden
- Tag
- Demand
- Details
- DID
- Direktor
- diskutiert
- Verteilung
- do
- erledigt
- Fahren
- zwei
- einfacher
- eingebettet
- Emissionen
- ermutigen
- genug
- Ganz
- insbesondere
- Jedes
- jeden Tag
- alles
- Beispiel
- Excel
- Exekutive
- Führungskräfte
- erklärt
- Erklärt
- umfangreiche
- konfrontiert
- Anlagen
- Faktoren
- füllen
- konzentriert
- Lebensmittel
- Aussichten für
- Zwingen
- unten stehende Formular
- Frei
- Fracht
- für
- voller
- voll
- weiter
- bekommen
- bekommen
- ABSICHT
- Go
- Kundenziele
- gehen
- Waren
- groß
- hätten
- passieren
- Los
- Haben
- he
- Hauptsitz
- Unternehmen
- hier (auf dänisch)
- GUTE
- Besondere
- Ultraschall
- aber
- HTTPS
- i
- if
- Umsetzung
- wichtig
- zu unterstützen,
- Verbesserung
- in
- inklusive
- Einschließlich
- Erhöhung
- Energiegewinnung
- Einblicke
- sofort
- in
- Investition
- Problem
- IT
- Jennifer
- Reise
- Juni
- nur
- Wesentliche
- grosse
- Nachname
- Letztes Jahr
- führenden
- LERNEN
- Verlassen
- geführt
- Rechtlich
- leicht
- wahrscheinlich
- Einschränkungen
- Grenzen
- wenig
- Belastung
- Ladeprogramm
- Belastungen
- Logistik
- suchen
- Los
- senken
- um
- Manager
- manuell
- Herstellung
- viele
- max-width
- Maximieren
- maximal
- Mitglied
- Mitglieder
- Metrik
- Monat
- mehr
- vor allem warme
- meist
- schlauer bewegen
- sollen
- erforderlich
- nicht
- jetzt an
- Anzahl
- of
- vorgenommen,
- on
- EINEM
- einzige
- Eröffnung
- Einkauf & Prozesse
- Gelegenheit
- Optimierung
- optimiert
- or
- Andere
- UNSERE
- übrig
- Gesamt-
- Partner
- für
- Ort
- Pläne
- Plato
- Datenintelligenz von Plato
- PlatoData
- Spieler
- Aufgabenstellung:
- Probleme
- verarbeitet
- Produkt
- Produkte
- setzen
- Qualität
- Quartal
- Fragen
- Direkt
- Angebot
- schnell
- Grund
- Gründe
- Empfehlungen
- Veteran
- Reduktion
- Grüße
- Vorschriften
- Forschungsprojekte
- Befragte
- Einzelhandel
- Rückkehr
- Reis
- robust
- Said
- Vertrieb
- Ersparnisse
- sah
- sagt
- sehen
- mehrere
- von Locals geführtes
- Shares
- Versand
- Short
- erklären
- Seite
- einfach
- So
- Software
- Lösung
- Lösungen
- einige
- etwas
- Raumfahrt
- Spanien
- verbringen
- gestapelt
- Standard
- begonnen
- Bundesstaat
- Tochtergesellschaft
- so
- liefern
- Supply Chain
- sicher
- Umfrage
- befragten
- Nachhaltigkeit
- sprechen
- Technologie
- als
- zur Verbesserung der Gesundheitsgerechtigkeit
- Das
- die Welt
- ihr
- Sie
- Dort.
- vom Nutzer definierten
- Ding
- Dritte
- fehlen uns die Worte.
- diejenigen
- nach drei
- Zeit
- zu
- tom
- auch
- Werkzeug
- Tracking
- Trailer
- Ausbildung
- , des Transports
- Trucking
- Wagenladung
- Trucks
- Wahrheit
- fluktuation
- Letztlich
- -
- Verwendung von
- Wert
- verschiedene
- sehr
- Video
- vs
- warten
- Warehouse
- wurde
- Ansehen
- we
- Gewicht
- GUT
- ging
- waren
- Was
- wann
- welche
- WHO
- Wild
- mit
- Worte
- weltweit wie ausgehandelt und gekauft ausgeführt wird.
- würde
- Jahr
- Jahr
- U
- Ihr
- Youtube
- Zephyrnet