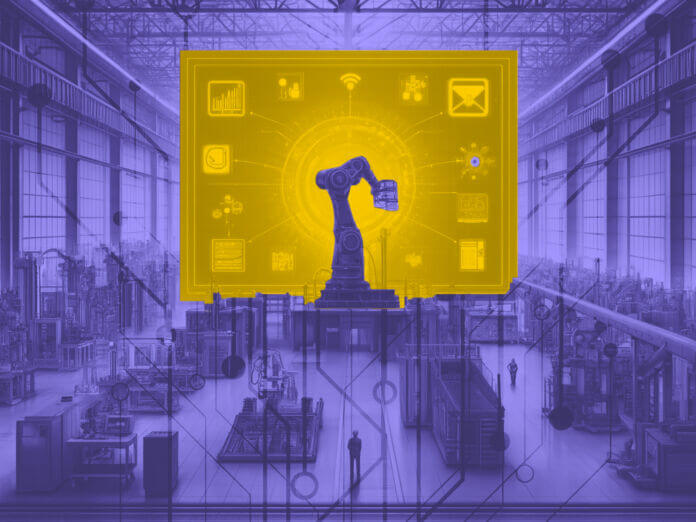
Digital transformation in manufacturing and machining marks a revolutionary shift toward integrating digital technologies into all aspects of business operations. This shift is particularly relevant for machine shops, where adopting such technologies can improve precision, speed, and quality.
Connectivity and the Internet of Things (IoT) stand at the heart of this modern manufacturing landscape. They enable machine shops to achieve unprecedented data exchange and automation levels. Through IoT, machines can communicate to facilitate real-time monitoring, predictive maintenance, and agile decision-making. This digital backbone transforms machine shops into more responsive, efficient, and competitive businesses in the global market.
The Evolution of Machine Shops
Traditional machine shops have historically relied on manual labor and standalone machinery. These operations are characterized by extensive paperwork, isolated systems, and limited real-time data analysis. Traditional setups face challenges such as inefficiency, high error rates, and difficulties in scaling operations or adapting to market demands.
Further, the manufacturing industry must overcome a daunting task — filling at least 4 million jobs by 2030. And this challenge is further exacerbated by a skills gap and an aging workforce. In this context, digital transformation emerges as a vital catalyst for change in the machining industry.
Integrating digital technologies — like IoT, AI, and cloud computing — allows machine shops to counter traditional operational challenges, enhance productivity, and attract a new generation of tech-savvy workers. This approach aligns companies with the evolving demands of the global market and workforce trends.
Key Technologies Driving Change
IoT devices are pivotal in machining and manufacturing by enabling real-time data collection from machinery and equipment. It provides invaluable insights into operational efficiency, machine health, and production quality. Cloud computing enhances this continuous stream of data. It offers vast storage capacities and powerful analytics tools to process and analyze data on an unprecedented scale.
Significantly, the global market for industrial IoT has seen robust growth, reaching over $544 billion in 2022, with projections suggesting it could surpass $1 trillion by 2025. It underscores the importance of technology in modern manufacturing industries.
Moreover, integrating AI and machine learning into these ecosystems revolutionizes maintenance and operational optimization. These technologies can predict equipment failures before they occur and suggest the most efficient production pathways, which reduces downtime and enhances productivity.
Impact on Operation and Efficiency
Digital tools significantly enhance operational efficiency in manufacturing through the automation of routine tasks and optimized resource management. It allows machine shops to allocate human and material resources more effectively.
In addition, predictive maintenance from AI and machine learning algorithms reduces downtime. It forecasts equipment malfunctions before they occur to prevent costly interruptions and extend machinery life.
Further, these advanced technologies enable manufacturers to customize production processes in real time and swiftly adapt to specific demands and changes in the market. This flexibility improves customer satisfaction by delivering tailor-made solutions and enhances manufacturing operations’ agility and competitiveness.
Enhancing Quality and Precision
Connectivity within modern machine shops enables more precise monitoring and control of machinery. For example, computer numerical control can develop highly accurate parts through fully autonomous equipment. This precision can come with comprehensive data analysis, which scrutinizes every aspect of the production process to ensure optimal performance and product quality.
Digital tools and technologies are crucial in this environment. They offer sophisticated quality control measures that were previously unattainable. These tools can identify even the slightest deviations from the desired quality standards by continuously analyzing data collected in real time. This oversight ensures the final products often exceed the stringent quality expectations of today’s markets.
Economic Benefits and ROI
The digital transformation of machine shops heralds significant cost savings through various channels, notably in energy consumption and waste reduction. Optimizing machine operations and streamlining processes allows digital tools to lower energy costs and minimize material waste. This approach contributes to economic savings and environmental sustainability.
Additionally, automation stands out as a game-changer, with predictions indicating it could reduce labor costs by 20 percent by 2025. Machines can take over repetitive and labor-intensive tasks and free up human workers for more complex and value-added activities. This shift cuts expenses and enhances production quality and efficiency to pave the way for increased revenue.
While substantial, initial investment in digital technologies promises a compelling return on investment for machine shops. By integrating advanced analytics, IoT, and automation tools can reduce operational costs and drive business growth through improved product quality and faster turnaround times. It demonstrates that the move toward digitalization is not merely a cost but a strategic investment in a shop’s future profitability and competitiveness.
Improving Worker Safety and Productivity
Digital transformation contributes to safer working environments in machine shops and manufacturing plants by leveraging enhanced monitoring capabilities and predictive alerts. These technologies can anticipate potential hazards and system failures to reduce the risk of accidents and injuries.
Considering that there were over 5,400 fatal work injuries in the U.S. in 2022, the importance of such advancements is paramount. Beyond improving safety, digital connectivity fosters a more productive workforce by providing employees with easier access to information and training resources.
Through intuitive interfaces and real-time data, workers can quickly learn new skills, adapt to changing operational requirements, and make informed decisions. It boosts efficiency and productivity and empowers employees to take proactive steps in maintaining their safety and well-being. Moreover, it underscores the profound impact of digital transformation on the modern workplace.
Embracing the Digital Future in Machine Shops
Machine shop owners and stakeholders stand at the brink of an unprecedented opportunity to revolutionize their operations, enhance safety, and secure their competitive edge through digital transformation. Embracing these changes and investing in digital solutions today will address current challenges and pave the way for a future of innovation, efficiency, and sustained growth in the evolving manufacturing landscape.
- SEO Powered Content & PR Distribution. Get Amplified Today.
- PlatoData.Network Vertical Generative Ai. Empower Yourself. Access Here.
- PlatoAiStream. Web3 Intelligence. Knowledge Amplified. Access Here.
- PlatoESG. Carbon, CleanTech, Energy, Environment, Solar, Waste Management. Access Here.
- PlatoHealth. Biotech and Clinical Trials Intelligence. Access Here.
- Source: https://www.iotforall.com/digital-transformation-and-connectivity-in-the-machine-shop
- :has
- :is
- :not
- :where
- $UP
- 1
- 20
- 2022
- 2025
- 4
- 400
- 5
- a
- access
- accidents
- accurate
- Achieve
- activities
- adapt
- adapting
- addition
- address
- Adopting
- advanced
- advancements
- agile
- Aging
- AI
- Alerts
- algorithms
- Aligns
- All
- allocate
- allows
- an
- analysis
- analytics
- analyze
- analyzing
- and
- anticipate
- approach
- ARE
- AS
- aspect
- aspects
- At
- attract
- Automation
- autonomous
- Backbone
- before
- benefits
- Beyond
- Billion
- boosts
- brink
- business
- business operations
- businesses
- but
- by
- CAN
- capabilities
- capacities
- Catalyst
- challenges
- change
- Changes
- changing
- channels
- characterized
- Cloud
- cloud computing
- collected
- collection
- come
- communicate
- Companies
- compelling
- competitive
- competitiveness
- complex
- comprehensive
- computer
- computing
- Connectivity
- consumption
- context
- continuous
- continuously
- contributes
- control
- Cost
- cost savings
- costly
- Costs
- could
- Counter
- crucial
- Current
- customer
- Customer satisfaction
- customize
- cuts
- data
- data analysis
- Data Exchange
- Decision Making
- decisions
- delivering
- demands
- demonstrates
- desired
- develop
- Devices
- difficulties
- digital
- digital technologies
- Digital Transformation
- digitalization
- downtime
- drive
- driving
- easier
- Economic
- Ecosystems
- Edge
- effectively
- efficiency
- efficient
- embracing
- emerges
- employees
- empowers
- enable
- enables
- enabling
- energy
- Energy Consumption
- enhance
- enhanced
- Enhances
- ensure
- ensures
- Environment
- environmental
- Environmental Sustainability
- environments
- equipment
- error
- Even
- Every
- evolution
- evolving
- example
- exceed
- exchange
- expectations
- expenses
- extend
- extensive
- Face
- facilitate
- failures
- faster
- final
- Flexibility
- For
- forecasts
- fosters
- Free
- from
- fully
- further
- future
- game-changer
- gap
- generation
- Global
- global market
- Growth
- Have
- Health
- Heart
- heralds
- High
- highly
- historically
- HTTPS
- human
- identify
- Impact
- importance
- improve
- improved
- improves
- improving
- in
- increased
- indicating
- industrial
- Industrial IoT
- industries
- industry
- inefficiency
- information
- informed
- initial
- Innovation
- insights
- Integrating
- interfaces
- Internet
- internet of things
- into
- intuitive
- invaluable
- investing
- investment
- iot
- isolated
- IT
- jpg
- labor
- landscape
- LEARN
- learning
- least
- levels
- leveraging
- Life
- like
- Limited
- lower
- machine
- machine learning
- machinery
- Machines
- maintaining
- maintenance
- make
- malfunctions
- management
- manual
- Manufacturers
- manufacturing
- manufacturing industry
- Market
- Markets
- material
- max-width
- measures
- merely
- million
- minimize
- Modern
- monitoring
- more
- Moreover
- most
- move
- must
- New
- notably
- numerical
- occur
- of
- offer
- often
- on
- operation
- operational
- Operations
- Opportunity
- optimal
- optimization
- optimized
- optimizing
- or
- out
- over
- Overcome
- Oversight
- owners
- paperwork
- Paramount
- particularly
- pathways
- pave
- performance
- pivotal
- plants
- plato
- Plato Data Intelligence
- PlatoData
- potential
- powerful
- precise
- Precision
- predict
- Predictions
- predictive
- prevent
- previously
- Proactive
- process
- processes
- Product
- Product Quality
- Production
- productive
- productivity
- Products
- profitability
- profound
- projections
- promises
- provides
- providing
- quality
- quickly
- Rates
- real
- real-time
- real-time data
- reduce
- reduces
- reduction
- relevant
- repetitive
- Requirements
- resource
- Resources
- responsive
- return
- revenue
- revolutionary
- revolutionize
- revolutionizes
- Risk
- robust
- routine
- s
- safer
- Safety
- satisfaction
- Savings
- Scale
- scaling
- secure
- seen
- shift
- Shop
- shops
- significant
- significantly
- skills
- skills gap
- Solutions
- sophisticated
- specific
- speed
- stakeholders
- stand
- standalone
- standards
- stands
- Steps
- storage
- Strategic
- STRATEGIC INVESTMENT
- stream
- streamlining
- stringent
- substantial
- such
- suggest
- surpass
- Sustainability
- sustained
- swiftly
- system
- Systems
- Take
- Task
- tasks
- Technologies
- Technology
- that
- The
- their
- There.
- These
- they
- things
- this
- Through
- time
- times
- to
- today
- today’s
- tools
- toward
- traditional
- Training
- Transformation
- transforms
- Trends
- Trillion
- u.s.
- underscores
- unprecedented
- various
- Vast
- vital
- Waste
- Way..
- were
- which
- will
- with
- within
- Work
- worker
- worker safety
- workers
- Workforce
- working
- Workplace
- zephyrnet