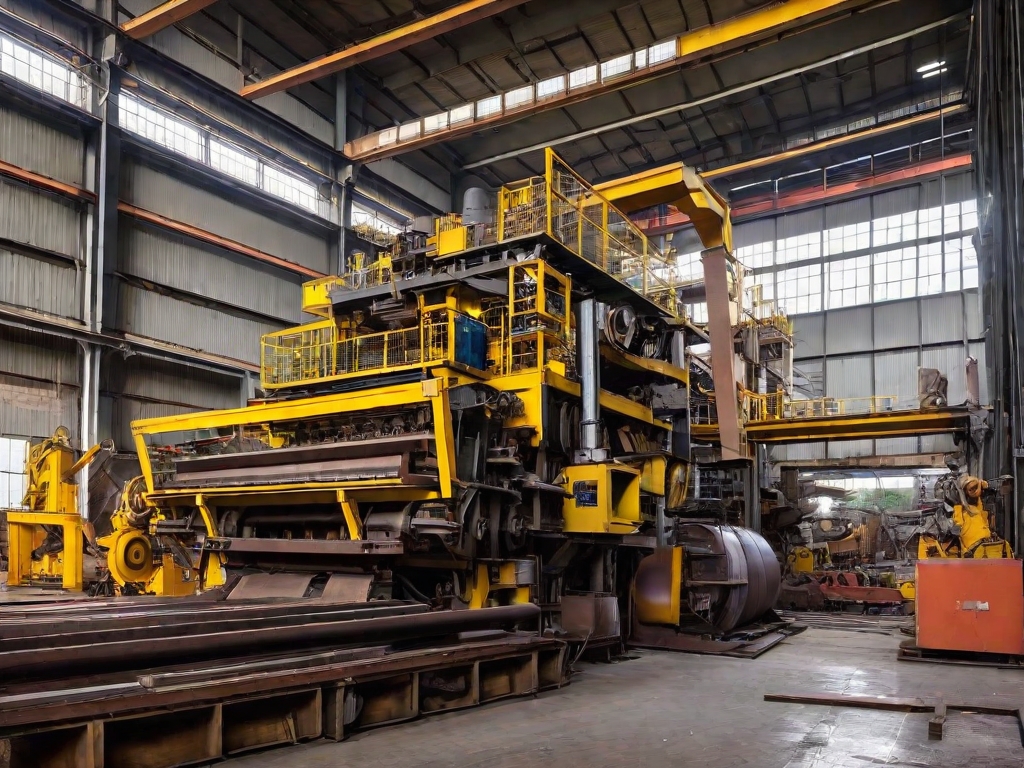
Australian company GreaseBoss has launched a flow meter designed to ensure appropriate machinery and equipment maintenance in manufacturing, mining, and utility applications. The ‘GreaseBoss Endpoint’ sensor is placed in line with grease points on machinery to monitor the flow of industrial lubricant. This helps companies remotely monitor their equipment, ensuring grease is being applied evenly and identifying any auto-lubricator reservoirs that require refilling. Sufficient lubrication is key for these applications, as increased friction can increase the amount of required maintenance and shorten the lifetime of equipment. Unplanned downtime of equipment can be expensive, making predictive maintenance highly beneficial.
Edge processing benefits
“The GreaseBoss system focuses on empowering small teams to remotely manage the greasing of massive fleets of machinery amongst other duties in their daily workflow,” said Peter Condoleon, CTO and co-founder of GreaseBoss.
GreaseBoss Endpoint integrates Nordic Semiconductor’s nRF52833 SoC for data collection and sensor interface management, before relaying key metrics to a GreaseBoss gateway using its Bluetooth low energy (LE) connectivity. The nRF52833 SoC’s 64 MHz, 32-bit Arm Cortex M4 processor with floating point unit (FPU) employs edge processing to select and send only the relevant information, avoiding unnecessary data transmission and conserving power.
From the gateway, the key data is relayed to the cloud, from where it can be accessed and analysed by users. Both automated and on-demand reports are available from the ‘GreaseBoss Cloud’ web platform, allowing companies to check whether they are meeting their pre-set lubrication requirements and receive alerts if any areas of non-compliance are detected. Users can also configure the plant structure set up from the web platform.
This system is built using Nordic solution partner Memfault’s IoT reliability platform for embedded observability, remote debugging, and over-the-air (OTA) fleet management. Memfault provides capabilities such as metric, reboot, and trace reporting along with performance benchmarking to ensure the reliability of the GreaseBoss Endpoint sensors.
By leveraging Memfault, GreaseBoss Endpoint reduces the need for unnecessary on-site visits and hardware returns to debug issues. It also helps users increase the uptime and reliability of their assets. With Memfault also used on its devices in development, GreaseBoss performs quality analysis and ensures each device meets the required standards before shipping.
Reduced power consumption
“To make GreaseBoss possible, our sensors needed to have the longest possible life while in harsh industrial environments with extreme temperatures and lots of RF obstacles,” said Condoleon. “The nRF52833 SoC hits the sweet spot with its ultra-low power consumption, extended operating temperature range from -40 to 105˚C and max transmit power of +8 dBm. The wide input voltage range also helped simplify the design and remove unnecessary components from the bill of materials (BOM) by powering the chip directly off the replaceable coin cell battery.”
Due to the large number of sensors required, and their often hazardous or hard-to-reach placement, achieving a long battery life was key to this application. The GreaseBoss Endpoint achieved this, partly due to the energy-efficient nature of the nRF52833 SoC and the performance monitoring capabilities of Memfault. GreaseBoss also used the Nordic Power Profiler Kit II (PPK2) to run various power consumption scenarios to ensure that the devices can continuously function for several years.
“The great community, support, and development tools were key drivers in choosing a Nordic solution,” continued Condoleon. “We used the nRF Connect SDK to build our application entirely in-house – in fact, we were able to use the SDK to prototype parts of our application in a matter of days and develop a field-ready beta [solution] in weeks. The abundance of sample code made it easy to get started, and we found the documentation easy to navigate and helpful as we started to optimise for power and performance.”
- SEO Powered Content & PR Distribution. Get Amplified Today.
- PlatoData.Network Vertical Generative Ai. Empower Yourself. Access Here.
- PlatoAiStream. Web3 Intelligence. Knowledge Amplified. Access Here.
- PlatoESG. Carbon, CleanTech, Energy, Environment, Solar, Waste Management. Access Here.
- PlatoHealth. Biotech and Clinical Trials Intelligence. Access Here.
- Source: https://www.iot-now.com/2023/10/30/139510-greaseboss-introduces-flow-meter-for-industrial-lubrication-monitoring/
- :has
- :is
- :where
- $UP
- a
- Able
- abundance
- accessed
- achieved
- achieving
- Alerts
- Allowing
- along
- also
- amongst
- amount
- an
- analysis
- and
- any
- Application
- applications
- applied
- appropriate
- ARE
- areas
- ARM
- AS
- Assets
- Automated
- available
- avoiding
- battery
- Battery life
- BE
- before
- being
- benchmarking
- beneficial
- benefits
- beta
- Bill
- both
- build
- built
- business
- by
- CAN
- capabilities
- cell
- check
- chip
- choosing
- Cloud
- Co-founder
- code
- Coin
- collection
- COM
- community
- Companies
- company
- components
- Connect
- Connectivity
- consumption
- continued
- continuously
- cortex
- CTO
- daily
- data
- Days
- Design
- designed
- detected
- develop
- Development
- development tools
- device
- Devices
- directly
- documentation
- downtime
- drivers
- due
- each
- easy
- Edge
- embedded
- employs
- empowering
- enabled
- Endpoint
- energy
- ensure
- ensures
- ensuring
- entirely
- environments
- equipment
- evenly
- expensive
- extreme
- fact
- FLEET
- fleet management
- floating
- flow
- focuses
- For
- found
- friction
- from
- function
- gateway
- get
- great
- Hardware
- Have
- helped
- helpful
- helps
- highly
- Hits
- How
- How To
- HTTPS
- identifying
- if
- ii
- in
- Increase
- increased
- industrial
- information
- input
- Integrates
- Interface
- Introduces
- iot
- issues
- IT
- ITS
- jpg
- Key
- kit
- large
- launched
- leveraging
- Life
- lifetime
- Line
- Long
- lots
- Low
- machinery
- made
- maintenance
- make
- Making
- manage
- management
- manufacturing
- massive
- materials
- Matter
- max
- meeting
- Meets
- metric
- Metrics
- Mining
- Monitor
- monitoring
- Nature
- Navigate
- Need
- needed
- news
- now
- number
- obstacles
- of
- off
- often
- on
- On-Demand
- only
- operating
- optimise
- or
- Other
- our
- partner
- parts
- performance
- performs
- Peter
- placed
- placement
- plant
- platform
- plato
- Plato Data Intelligence
- PlatoData
- Point
- points
- possible
- power
- Powering
- predictive
- processing
- Processor
- prototype
- provides
- quality
- range
- receive
- reduces
- relevant
- reliability
- remote
- remove
- Reporting
- Reports
- require
- required
- Requirements
- returns
- Run
- Said
- scenarios
- sdk
- send
- sensors
- set
- several
- Shipping
- simplify
- small
- solution
- Spot
- standards
- started
- structure
- such
- support
- sweet
- system
- teams
- that
- The
- their
- These
- they
- this
- to
- tools
- trace
- transmit
- unit
- unnecessary
- uptime
- use
- used
- users
- using
- utility
- various
- Visits
- Voltage
- was
- we
- web
- Weeks
- were
- whether
- while
- wide
- with
- workflow
- years
- zephyrnet