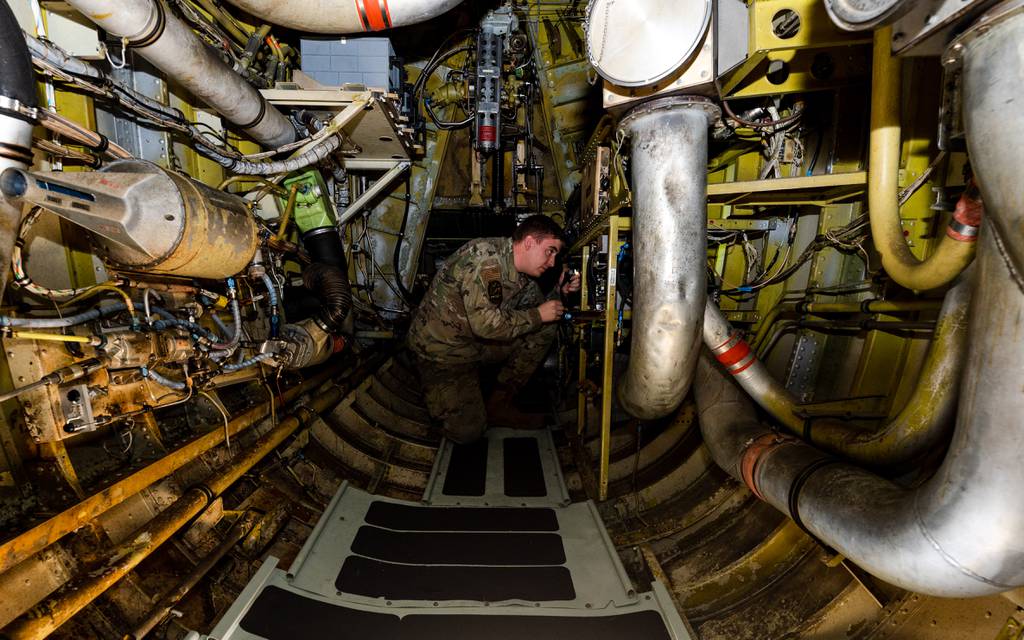
BARKSDALE AIR FORCE BASE, La. — As the B-52H Stratofortress tops more than six decades in service, it’s grown increasingly temperamental — and for the U.S. Air Force, a challenge to keep in the air.
Its original 1960s-era engines keep finding “new and creative” ways to break, as an Air Force Global Strike Command leader put it. Stocks of spare parts are limited, and the industrial base needed to repair broken components or make new ones is drying up.
The Air Force is scrambling to keep the B-52 bomber operational and is resorting to an array of options to do so — up to and including a process called cannibalization. To date, three out of every five B-52s are able to carry out their missions at any given time.
Airmen across the spectrum at Barksdale Air Force Base — from the flight line and supply shop to leadership — describe a situation where maintainers must regularly “cannibalize” parts, meaning take them off one B-52 to be installed on another so the second aircraft can fly.
It’s a lengthy process that can create further problems, and it’s meant to be a last resort. But the B-52 community is increasingly turning to that method. Tech. Sgt. Bonny Carter, the noncommissioned officer in charge of the B-52′s decentralized maintenance support section at Barksdale, said the rate of cannibalization has gone up 200% since 2019, before the coronavirus pandemic snarled supply chains worldwide.
Global Strike Command disputed that figure, though it acknowledged cannibalization rose over the last five years mainly due to obsolete parts. The command did not provide statistics on cannibalization rates, as requested by Defense News.
The Air Force is using other fallback options first, such as pulling parts out of the “Boneyard,” the Air Force’s airplane cemetery in Arizona where many retired B-52s rest. The service also combs the industrial base for new sources of fresh parts, and taps its own back shops and sustainment center to repair parts or make new ones. Back shops are rooms where specialized repair and maintenance is done on smaller components.
A wide-ranging series of modernizations for the B-52 — everything from new Rolls-Royce engines to new wheels and brakes — is on the way, and the Air Force hopes these upgrades will result in a more reliable airplane, with a fresh supply of spare parts that relieves some pressure on maintainers.
But until that happens, Global Strike Command will need to keep the B-52H flying, even if it’s increasingly daunting, said Col. David Miller, the organization’s director of logistics and engineering.
Vendors, pool of parts dwindling
The biggest maintenance challenge facing the B-52 is the “slow atrophy” of the defense-industrial base that supplies it, according to Miller.
“The vendor base is just drying up,” he said. “Trying to entice vendors to continue to make very old, very difficult parts in small numbers is a challenge,” particularly when it comes to specialized parts with little, if any, value to commercial aviation.
The reduction of the B-52 fleet over the years — from a high of 744 to 76 today — also shrunk the market for spare parts, further limiting companies’ opportunities to make money in this business. Some companies, particularly small mom-and-pop shops, have either decided to stop making parts the B-52 relies upon, or gone out of business entirely.
It can take months or even years for a B-52 to get crucial parts. One part, a valve, has a 900-day lead time, Miller’s office said, and his directorate is working to replace that rare piece with a more readily available valve.
Global Strike Command said it sometimes takes those valves off B-52s entering depot maintenance in order to install them on bombers preparing to fly.
The parts supply problem is particularly acute for the B-52′s TF33 engines, which Pratt & Whitney made in the 1960s, Miller said. Parts from those engines — or whole engines entirely — are the component most often cannibalized for B-52s, he said.
Miller noted the bomber depot at the Oklahoma City Air Logistics Complex used to regularly remove engines from B-52s as they entered their lengthy heavy maintenance process, then reinstall those components on other B-52s that were nearly finished with their overhauls. But with more spare parts on the depot shelves, the service no longer does that.
The Rolls-Royce F130 engines are to come with new parts that last longer before they break or require maintenance, as well as a fresh supply chain making readily available replacements when parts do break, he explained.
“What we’re buying into is an aircraft that’s not going to have to go through core maintenance very often, if at all,” Miller said. “As opposed to the TF33 — that goes through a lot of maintenance right now.”
The Pentagon in November moved to shore up the B-52′s engines, awarding Pratt & Whitney a contract worth up to $870 million to sustain nearly 1,000 TF33s. Those engines also power the E-3 Sentry airborne warning and control aircraft, and the sustainment contract could run through spring 2034.
In an interview with Defense News at the time of the contract’s award, Pratt & Whitney executive Caroline Cooper said the sustainment contract would help address the spare parts shortages exacerbated by the decline of companies making niche, low-volume parts for the B-52. Cooper said this deal provides funding for the firm to either make those parts itself or find other companies to take on the work.
“We’re looking at … the operational tempo of the aircraft, and then looking at the inherent risks in the supply chain, and wanted to build that upper limit so that we can move quickly and expeditiously to get the men and women in the Air Force what they need,” Cooper said in November.
Master Sgt. Dylan Drake, a production superintendent at Barksdale’s 2nd Maintenance Squadron, said maintainers are “excited” for the new engines to come online. If they’re as reliable as promised, he said, maintainers will be able to turn their attention to other parts of the B-52.
“If we don’t have to worry about the engines, that’ll let us focus on other systems,” Drake said.
When maintainers remove faulty parts from the B-52, Miller said, sometimes they can be overhauled or repaired — but they sometimes must be replaced entirely. And that is growing harder and harder.
Carter, of the 2nd Logistics Readiness Squadron, said when a maintainer needs a spare part, the first step is to look in her supply shop’s own stocks, then reach out to other supply shops elsewhere if it’s not on the shelf. The decentralized maintenance support section Carter oversees stores and organizes spare parts for maintainers to fix Barksdale’s B-52s.
If they’re still striking out, the Air Force has workarounds, Miller and Carter said in separate interviews. That could include turning to an Air Force back shop to make a new part or the Air Force Sustainment Center at Tinker Air Force Base in Oklahoma.
Miller said the components undergoing production or overhaul at the sustainment center range from wire harnesses to larger, modular components known as line replaceable units.
The advantage of keeping the Air Force’s own industrial base for B-52 parts humming, Miller noted, is that the service knows it will be available if a war breaks out.
“You never know when we’re going to be called upon, perhaps in a wartime environment, to be able to provide that [maintenance in] real time,” he said. “That’s not the time to go out and find we’ve got to cold start [the production line], and [with] an 18-month delay, having a new vendor produce something for us.”
But the work is also stretching the service further. Carter said back shop airmen are working longer hours to fix broken parts — even those that previously weren’t their responsibility to repair.
It could mean pulling a part out of a retired B-52 in the Boneyard, officially known as the 309th Aerospace Maintenance and Regeneration Group. But there are a finite number of B-52s there the service can scavenge, Carter said, so that solution will only work for so long.
It could mean hunting down a commercial company that does similar kinds of work and hiring them to make a part.
And if all else fails, airmen pull parts from one aircraft for installation on another. But that solution can make more problems.
“When we do the cannibalization, it downs another aircraft so we can make this aircraft flyable to conduct its mission, to get training hours,” Carter said. “And then we have to swap again. We are constantly swapping parts.”
“But we’re learning to work with what we got,” she added. “You know, more with less.”
Stephen Losey is the air warfare reporter for Defense News. He previously covered leadership and personnel issues at Air Force Times, and the Pentagon, special operations and air warfare at Military.com. He has traveled to the Middle East to cover U.S. Air Force operations.
- SEO Powered Content & PR Distribution. Get Amplified Today.
- PlatoData.Network Vertical Generative Ai. Empower Yourself. Access Here.
- PlatoAiStream. Web3 Intelligence. Knowledge Amplified. Access Here.
- PlatoESG. Carbon, CleanTech, Energy, Environment, Solar, Waste Management. Access Here.
- PlatoHealth. Biotech and Clinical Trials Intelligence. Access Here.
- Source: https://www.defensenews.com/air/2024/02/12/more-with-less-lacking-parts-airmen-scramble-to-keep-b-52s-flying/
- :has
- :is
- :not
- :where
- $UP
- 000
- 1
- 10
- 11
- 11th
- 12
- 16
- 1st
- 2%
- 2019
- 2023
- 2024
- 2nd
- 4
- 5
- 7
- 70
- 8
- 9
- a
- Able
- About
- According
- acknowledged
- across
- acute
- added
- address
- ADvantage
- Aerospace
- again
- AIR
- Air Force
- aircraft
- Airplane
- All
- also
- an
- and
- Andersen
- Another
- any
- April
- ARE
- arizona
- Array
- AS
- assigned
- At
- attention
- available
- aviation
- B-52
- back
- base
- BE
- been
- before
- Biggest
- bomb
- Break
- breaks
- Broken
- build
- business
- but
- Buying
- by
- called
- CAN
- caroline
- carry
- Center
- chain
- chains
- challenge
- charge
- check
- City
- class
- cold
- COM
- come
- comes
- commercial
- community
- Companies
- company
- complex
- component
- components
- Conduct
- constantly
- continue
- contract
- control
- cooper
- Core
- Coronavirus
- could
- cover
- covered
- create
- crucial
- Date
- David
- deal
- decades
- decentralized
- decided
- Decline
- Defense
- delay
- describe
- DID
- difficult
- Director
- do
- does
- done
- Dont
- down
- downs
- drake
- due
- East
- either
- else
- elsewhere
- Engine
- Engineering
- Engines
- entered
- entering
- entirely
- Environment
- Ether (ETH)
- Even
- Every
- everything
- executive
- explained
- facing
- fails
- false
- faulty
- Figure
- Find
- finding
- finite
- Firm
- First
- five
- Fix
- FLEET
- flight
- flying
- Focus
- For
- Force
- fresh
- from
- funding
- further
- get
- given
- Global
- Go
- Goes
- going
- gone
- got
- Group
- Growing
- grown
- happens
- harder
- harnesses
- Have
- having
- he
- heavy
- help
- her
- here
- High
- Hiring
- his
- hopes
- HOURS
- HTTPS
- Hunting
- if
- image
- images
- in
- include
- Including
- increasingly
- industrial
- inherent
- install
- installation
- installed
- Interview
- Interviews
- into
- issues
- IT
- ITS
- itself
- Jan
- jpg
- just
- Keep
- keeping
- kinds
- Know
- known
- knows
- la
- lacking
- lands
- larger
- Last
- lead
- leader
- Leadership
- learning
- left
- less
- let
- LIMIT
- Limited
- limiting
- Line
- little
- logistics
- Long
- longer
- Look
- looking
- Lot
- made
- mainly
- maintenance
- make
- make money
- Making
- many
- Market
- May..
- mean
- meaning
- meant
- Men
- method
- Michael
- Middle
- Middle East
- Military
- Miller
- million
- Mission
- missions
- modular
- money
- months
- more
- most
- move
- moved
- moves
- must
- nearly
- Need
- needed
- needs
- never
- New
- news
- niche
- no
- noted
- November
- now
- number
- numbers
- obsolete
- of
- off
- Office
- Officer
- Officially
- often
- Oklahoma
- Old
- on
- ONE
- ones
- online
- only
- operational
- Operations
- opportunities
- opposed
- Options
- or
- order
- organizes
- original
- Other
- out
- over
- Overhaul
- own
- part
- particularly
- parts
- pentagon
- perform
- perhaps
- Personnel
- piece
- pilot
- plato
- Plato Data Intelligence
- PlatoData
- pool
- power
- Prepare
- preparing
- pressure
- previously
- Problem
- problems
- process
- produce
- Production
- promised
- propulsion
- provide
- provides
- pulling
- put
- quickly
- range
- RARE
- Rate
- Rates
- reach
- readily
- Readiness
- real
- real-time
- reduction
- regeneration
- regularly
- reliable
- remove
- repair
- replace
- replaced
- reporter
- requested
- require
- Resort
- responsibility
- REST
- result
- right
- risks
- Rolls-Royce
- Rooms
- ROSE
- Run
- s
- Said
- Second
- Section
- senior
- separate
- Series
- service
- she
- Shelf
- shelves
- Shop
- shops
- shortages
- similar
- since
- situation
- SIX
- small
- smaller
- So
- solution
- some
- something
- sometimes
- Sources
- special
- specialized
- Spectrum
- spring
- start
- statistics
- Step
- Stephen
- Still
- Stocks
- Stop
- stores
- strike
- Student
- such
- supplies
- supply
- supply chain
- Supply chains
- support
- swap
- swapping
- Systems
- Take
- takes
- Taps
- tech
- Tempo
- than
- that
- The
- their
- Them
- then
- There.
- These
- they
- this
- those
- though?
- three
- Through
- time
- times
- to
- today
- Tops
- Training
- traveled
- true
- TURN
- Turning
- u.s.
- U.S. Air Force
- undergoing
- units
- until
- upgrades
- upon
- us
- used
- using
- value
- valve
- valves
- vendor
- vendors
- very
- Video
- Videos
- wanted
- war
- warning
- Way..
- ways
- we
- WELL
- were
- What
- when
- which
- whole
- will
- william
- Wing
- Wire
- with
- Women
- Work
- working
- worldwide
- worry
- worth
- would
- years
- zephyrnet