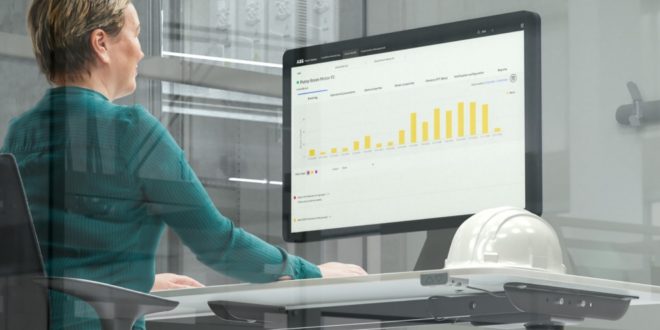
Energy has always been vital to industry but rising costs in recent year have emphasized that it is a strategically important resource that can impact profitability and competitiveness.
This was the key finding of a global survey of over 2,300 business leaders published by ABB in March 2023, with 92 percent of respondents indicating rising costs are a threat to their future planning. They made it clear that dealing with energy challenges will override spending plans that would normally enable their organization to remain competitive, whether that’s related to their workforces with recruitment, retaining or developing talent, or investing in new technology capabilities for greater productivity, agility and speed. Survey respondents also warned that rising energy costs may delay progress towards their decarbonization goals.
Energy in industry
Viewing energy as a resource rather than a cost can have significant benefits. There are multiple services and technology strategies that can help.
- Boosting the efficiency of industrial motors – electric motors are used in production and packaging lines, pumps, fans, cranes and conveyors, as well as heating, ventilation and air conditioning (HVAC) systems in the built environment. Improving their energy efficiency will cut consumption and as a result, will reduce costs and CO2 This makes motor efficiency a resource that the International Energy Agency (IEA) calls “first fuel” as it reduces the need to generate, transmit or distribute electricity and frees up capacity for other uses.
- Business energy consulting – a flexible service that can help with procurement and management of energy. A consultant can help with tightening up the energy use from lighting, appliances and temperature settings in building, as well as improving metering. They can also help businesses to deploy solar or wind power generation and energy storage.
- Power quality issues – some businesses may be consuming excess energy because of the electrical phenomena of low power factor and harmonics. Once identified, these are straightforward to solve with power factor correction equipment or harmonic filters.
- Energy management system (EMS) – a technology for monitoring and forecasting consumption, and automatically managing energy sources and loads to optimize consumption.
Focusing on motor efficiency
Around 70 percent of all the electricity consumed by industry is used by electric motors. That makes them a big target for cutting costs and decarbonizing. Businesses that operate a lot of electric motors should prioritize motor efficiency in their energy strategy.
A challenge is that without detailed knowledge of a motor’s operating parameters, it’s hard to know whether it is using more energy than it should be. That is compounded by the sheer number of motors in operation. A typical manufacturing or processing plant may have hundreds or thousands of motors and it’s been estimated that there are more than 300 million motors around the world.
Another factor is that while legislation governs the minimum efficiency standards for new motors, a motor may be in operation for decades and consume energy that is worth many multiples of its purchase cost.
Rather than simply accepting this ongoing cost, businesses can take action by adjusting operational parameters, upgrading existing motors to modern high-efficiency models, and / or installing variable speed drives (VSDs).
Energy audits draw on efficiency expertise
Before operators can take any action to improve motor efficiency, they need to know which motors to target. However, the main focus for most in-house maintenance technicians is uptime, machine availability and rectifying breakdowns, rather than energy efficiency.
It’s unlikely that in-house operators will be fully aware of the hidden financial and environmental costs of low efficiency in motors. Few technicians will have had in-depth training on motor efficiency standards, or on comparing the purchase price of a new high-efficiency motor with the value of energy saved by installing it.
This is why it’s worth partnering with service experts. Because they constantly work with motor data, experts in motor efficiency can cut through the noise. Their first step is to provide guidance for in-house operators to deploy data-gathering technology across their fleet to provide an energy efficiency audit. They will then review and analyse that data to quickly identify the least-efficient motors and provide costed actions.
The result is a picture of where excessive energy is used, as well as the cost and return on investment (ROI) of rectifying it. This data-driven insight makes it easy for an operations director to make an informed investment in saving energy.
Flooring manufacturer cuts consumption by 15 percent
Energy efficiency audits are already reaping rewards for some operators. For example, flooring manufacturer Tarkett partnered with ABB to identify energy-saving potential at its factory in Ronneby, Sweden.
Experts identified that by replacing 10 large motors with the latest ultra-premium efficiency motor-drive packages, Tarkett could cut the site’s overall electricity demand by 15 percent. This is equivalent to 800 megawatt-hours (MWh) per year for an investment with an ROI of 18 months.
The operator is now planning to extend data-gathering to uncover energy-saving opportunities in additional motors.
This approach that can be deployed in any industry that uses a large number of electric motors. By partnering with ABB, operators can cut through the complexity of data to quickly identify the energy savings that make the biggest impact on the bottom line.
- SEO Powered Content & PR Distribution. Get Amplified Today.
- PlatoData.Network Vertical Generative Ai. Empower Yourself. Access Here.
- PlatoAiStream. Web3 Intelligence. Knowledge Amplified. Access Here.
- PlatoESG. Automotive / EVs, Carbon, CleanTech, Energy, Environment, Solar, Waste Management. Access Here.
- BlockOffsets. Modernizing Environmental Offset Ownership. Access Here.
- Source: https://usgreentechnology.com/motor-efficiency-as-an-energy-resource/
- :has
- :is
- :where
- $UP
- 10
- 15%
- 2023
- 300
- 70
- a
- accepting
- across
- Action
- actions
- Additional
- agency
- AIR
- Air Conditioning
- All
- already
- also
- always
- an
- analyse
- and
- any
- appliances
- approach
- ARE
- around
- AS
- At
- audit
- audits
- automatically
- availability
- aware
- BE
- because
- been
- benefits
- Big
- Biggest
- Bottom
- Building
- built
- business
- businesses
- but
- by
- Calls
- CAN
- capabilities
- Capacity
- challenge
- challenges
- clear
- comparing
- competitive
- competitiveness
- complexity
- constantly
- consultant
- consulting
- consume
- consumed
- consumption
- Cost
- Costs
- could
- Cut
- cuts
- cutting
- data
- data-driven
- dealing
- decades
- decarbonization
- delay
- Demand
- deploy
- deployed
- detailed
- developing
- Director
- distribute
- draw
- drives
- easy
- efficiency
- Electric
- electricity
- emphasized
- enable
- energy
- energy efficiency
- energy use
- Environment
- environmental
- equipment
- Equivalent
- estimated
- example
- excess
- existing
- experts
- extend
- factor
- factory
- fans
- few
- filters
- financial
- finding
- First
- FLEET
- flexible
- Focus
- For
- from
- fully
- future
- generate
- generation
- Global
- Goals
- governs
- greater
- guidance
- had
- Hard
- Have
- help
- Hidden
- However
- HTTPS
- Hundreds
- hvac
- identified
- identify
- IEA
- Impact
- important
- improve
- improving
- in
- in-depth
- indicating
- industrial
- industry
- informed
- insight
- installing
- International
- investing
- investment
- issues
- IT
- ITS
- jpg
- Key
- Know
- knowledge
- large
- latest
- leaders
- Legislation
- Lighting
- Line
- lines
- loads
- Lot
- Low
- machine
- made
- Main
- maintenance
- make
- MAKES
- management
- management system
- managing
- Manufacturer
- manufacturing
- many
- March
- May..
- million
- minimum
- models
- Modern
- monitoring
- months
- more
- most
- Motor
- Motors
- multiple
- Need
- New
- Noise
- normally
- now
- number
- of
- on
- once
- ongoing
- operate
- operating
- operation
- operational
- Operations
- operator
- operators
- opportunities
- Optimize
- or
- organization
- Other
- over
- overall
- override
- packages
- packaging
- parameters
- partnered
- partnering
- percent
- picture
- planning
- plans
- plato
- Plato Data Intelligence
- PlatoData
- potential
- power
- price
- Prioritize
- processing
- procurement
- Production
- productivity
- profitability
- Progress
- provide
- published
- pumps
- purchase
- quality
- quickly
- rather
- recent
- recruitment
- reduce
- reduces
- related
- remain
- resource
- respondents
- result
- retaining
- return
- review
- Rewards
- rising
- ROI
- saving
- Savings
- service
- Services
- settings
- should
- significant
- simply
- solar
- SOLVE
- some
- Sources
- speed
- Spending
- standards
- Step
- storage
- straightforward
- Strategically
- strategies
- Strategy
- Survey
- Sweden
- system
- Systems
- Take
- Talent
- Target
- technicians
- Technology
- than
- that
- The
- the world
- their
- Them
- then
- There.
- These
- they
- this
- thousands
- threat
- Through
- tightening
- to
- towards
- Training
- transmit
- typical
- uncover
- unlikely
- uptime
- use
- used
- uses
- using
- value
- vital
- was
- WELL
- whether
- which
- while
- why
- will
- wind
- wind power
- with
- without
- Work
- world
- worth
- would
- year
- zephyrnet