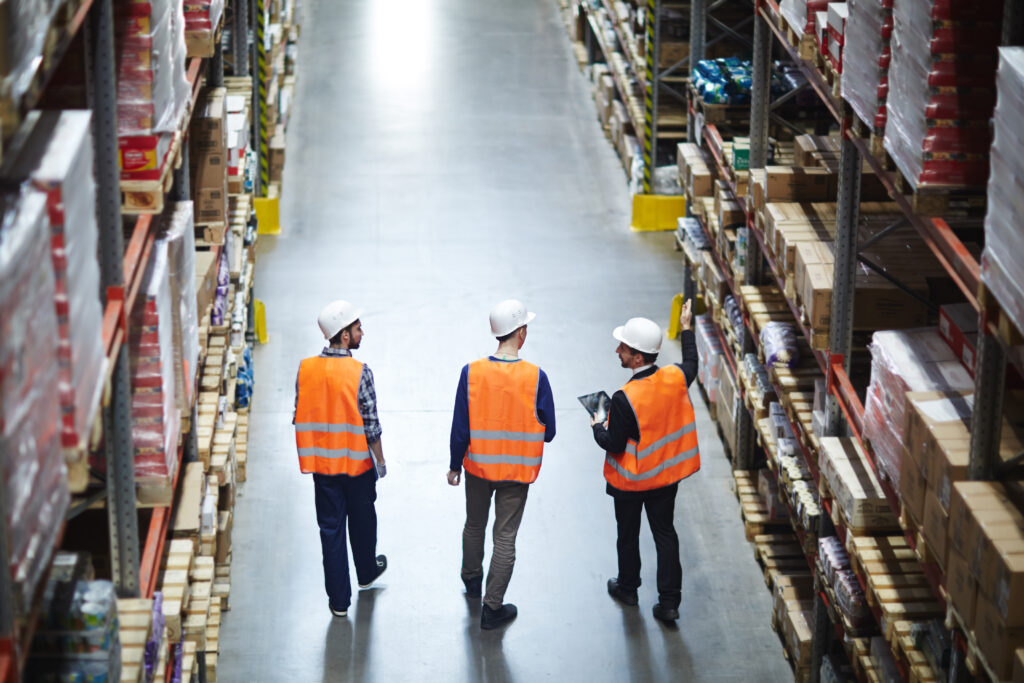
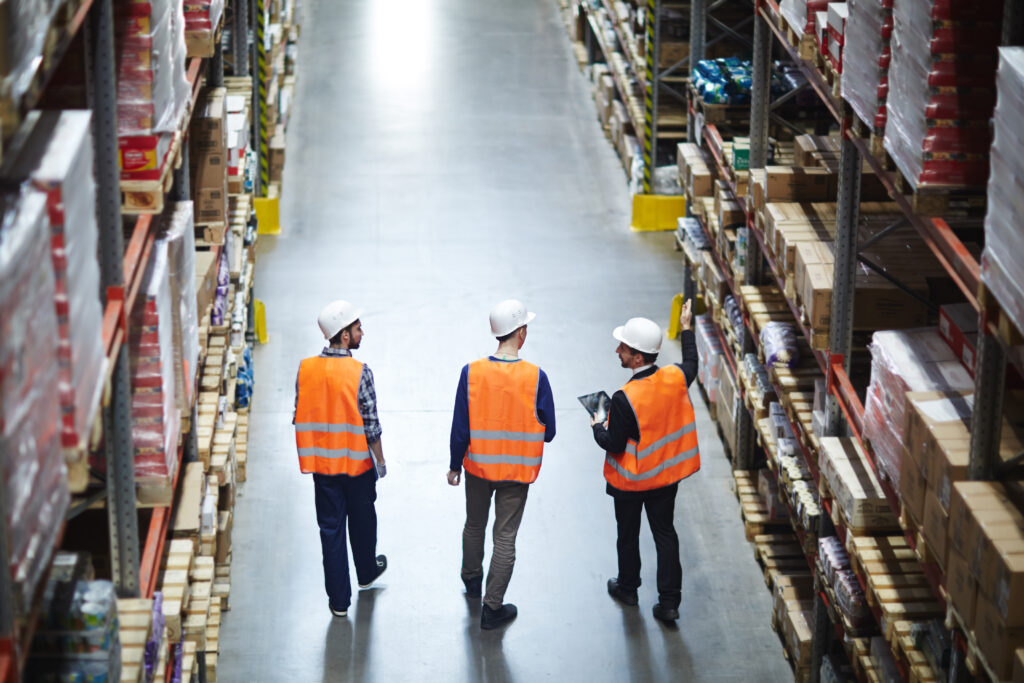
New research from Watco has highlighted the challenges faced by facilities management (FM) professionals in the warehousing and storage sector, and how they impact the ability to run safe and efficient operations
The research revealed that more than half (57%) have seen an increase in their workload over the past year. On top of this, over a third (38%) regularly go over budget on urgent repair work to remove hazards.
Despite these pressures, respondents from the warehousing and storage sector revealed that almost two thirds (61%) have had their budgets cut by up to 25% in the past year and a further fifth (21%) said that theirs had been cut by 26-50%. Worryingly, a third (33%) said that these budget cuts had posed a safety risk to their facility.
Scott Saunders, technical service manager at Watco, commented: “For FMs in this sector, large workloads are making it hard to conduct regular site inspections and carry out repairs, meaning small repair jobs are often deprioritised. However, minor surface damage can quickly grow into a much larger hazard when left to deteriorate. This increases the risk of accidents, but also the time and materials required to carry out the repair, which takes it over budget. Although difficult to implement in the short term, enforcing a structured approach to maintenance and repairs among the FM team with rotas and checklists will help to break the cycle. By prioritising those tasks, surface damage can be spotted and repaired at the earliest opportunity, reducing the hazards in the facility and eliminating time-consuming, expensive repair jobs.”
However, budget cuts are a contributing factor, rather than the risk to safety itself. Respondents revealed that the largest risks to health and safety within their business were:
- Time constraints
- Having to meet changing standards and legislation
- Fire safety
- Incorrect installations
- Faulty or damaged materials handling equipment
As well as featuring in the top five risks to health and safety, 43% of respondents revealed that the use of materials handling equipment (MHE) had resulted in an accident or near-miss at their business in the last year. The Health and Safety Executive (HSE) reported the main causes of accidents in warehousing and storage, including work at height; vehicles in and around the warehouse; and moving or falling objects.
Scott Saunders, technical service manager at Watco, continued: “Facilities managers cannot impact how changing legislation affects their responsibilities. Therefore, their time is best spent addressing the risks that they can control. Materials handling equipment that is damaged or being misused is incredibly dangerous because of the range of accidents it can cause. As highlighted by the HSE, accidents in this sector are commonly caused by the unexpected movement of objects and vehicles, which are strongly linked to the use of MHE. Using signage and line marking allows FMs to map out the warehouse with pathways and highlight hazardous areas which helps employees avoid hazards and increases efficiency.”
Almost half (46%) of respondents in the sector say it is difficult to find good employees and 30% often worry that there is a skills shortage. However, it’s clear they want to invest in overcoming skills gaps with 71% of respondents stating that they want to do more professional development.
The top five areas they would like more training and development are:
- Sustainability practices
- Product/technical
- Recruiting the right people
- Changes to industry legislation
- Risk reduction
Scott concludes: “Building teams with the skills and knowledge required in the sector today will significantly impact the safe and smooth running of warehouse and storage facilities. The research indicates that FMs understand this but finding the time and the budget to do so is proving a challenge. Those in the sector must lean on external support for this e.g. using third party resources to upskill the workforce on sustainability and legislation changes, sourcing documents to help with core FM tasks around repairs and maintenance or requesting expertise on products to make the facility safer and more efficient.”
For more information on the challenges facing the warehousing and logistics sector and tips from the experts, download Watco’s free one-page report here.
Read Similar…
- SEO Powered Content & PR Distribution. Get Amplified Today.
- PlatoData.Network Vertical Generative Ai. Empower Yourself. Access Here.
- PlatoAiStream. Web3 Intelligence. Knowledge Amplified. Access Here.
- PlatoESG. Carbon, CleanTech, Energy, Environment, Solar, Waste Management. Access Here.
- PlatoHealth. Biotech and Clinical Trials Intelligence. Access Here.
- Source: https://www.logisticsbusiness.com/materials-handling-warehousing/loading-bay-safety/overcoming-challenges-in-warehouse-safety-and-efficiency/
- :has
- :is
- $UP
- a
- ability
- accident
- accidents
- addressing
- affects
- allows
- almost
- also
- Although
- among
- an
- and
- approach
- ARE
- areas
- around
- AS
- At
- avoid
- BE
- because
- been
- being
- BEST
- Break
- budget
- Budgets
- business
- but
- by
- CAN
- cannot
- carry
- Cause
- caused
- causes
- challenge
- challenges
- Changes
- changing
- clear
- CO
- commented
- commonly
- concludes
- Conduct
- continued
- contributing
- control
- Core
- Cut
- cuts
- cycle
- damage
- Dangerous
- Development
- difficult
- do
- documents
- download
- e
- earliest
- efficiency
- efficient
- eliminating
- employees
- enforcing
- equipment
- Ether (ETH)
- executive
- expensive
- expertise
- experts
- external
- faced
- facilities
- Facility
- facing
- factor
- Falling
- Featuring
- fifth
- Find
- finding
- five
- For
- Free
- from
- further
- gaps
- Go
- good
- Grow
- had
- Half
- Handling
- Hard
- Have
- Health
- height
- help
- helps
- Highlight
- Highlighted
- How
- However
- HTTPS
- Impact
- implement
- in
- Including
- Increase
- Increases
- incredibly
- indicates
- industry
- information
- into
- Invest
- IT
- itself
- Jobs
- jpeg
- knowledge
- large
- larger
- largest
- Last
- Last Year
- lean
- left
- Legislation
- like
- Line
- linked
- logistics
- Main
- maintenance
- make
- Making
- management
- manager
- Managers
- map
- marking
- materials
- meaning
- Meet
- minor
- more
- more efficient
- movement
- moving
- much
- must
- objects
- of
- often
- on
- Opportunity
- or
- out
- over
- overcoming
- party
- past
- pathways
- plato
- Plato Data Intelligence
- PlatoData
- posed
- pressures
- Products
- professional
- professionals
- proving
- quickly
- range
- rather
- reducing
- regular
- regularly
- remove
- repair
- repairs
- report
- Reported
- required
- research
- Resources
- respondents
- responsibilities
- resulted
- Revealed
- right
- Risk
- risks
- Run
- running
- safe
- safer
- Safety
- Said
- Saunders
- say
- sector
- seen
- service
- Short
- shortage
- significantly
- site
- skills
- small
- smooth
- So
- Sourcing
- spent
- standards
- stating
- storage
- strongly
- structured
- support
- Surface
- takes
- tasks
- team
- teams
- Technical
- term
- than
- that
- The
- their
- There.
- therefore
- These
- they
- Third
- this
- those
- time
- time-consuming
- tips
- to
- today
- top
- Training
- two
- understand
- Unexpected
- urgent
- use
- using
- Vehicles
- want
- Warehouse
- Warehousing
- WELL
- were
- when
- which
- will
- with
- within
- Work
- Workforce
- worry
- would
- year
- zephyrnet