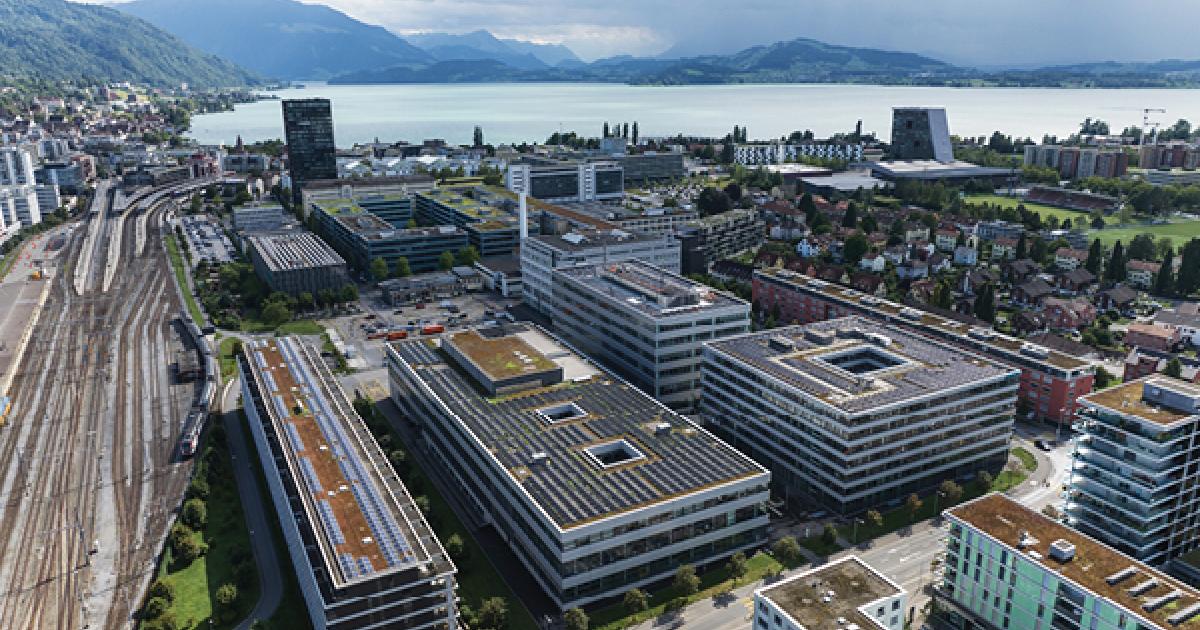
This article is sponsored by Siemens.
Moving in circles typically means a lack of progress, but in sustainability circularity means progress. This is particularly apparent in the construction industry — which consumes significant resources while producing a lot of waste. This means there’s also an opportunity to save huge amounts of valuable raw materials. And the scale of this challenge will only continue to grow with the global investment in the sector expected to increase by 85 percent to an impressive $17.5 trillion annually until 2030. New approaches and a holistic way of thinking are urgently needed.
Buildings and their environmental performance play a significant role in achieving decarbonization targets and taking sustainability action. However, for the real estate industry, the even more challenging paradigm shift is yet to come: the transition from a linear economy to circular construction in the planning, construction and operation of real estate.
By now, most sustainability professionals are familiar with the concept of a circular economy — the idea of a world without waste in which everything is recycled, every resource is reused and material lifecycles are almost completely closed far beyond conventional recycling.
In the construction sector, there is immense opportunity to view buildings as “material banks,” or sources of valuable materials that can be recovered and reused. From Day 1 of the planning, well before the first sod is turned, all options for re-use and recycling of the building materials should be considered and integrated.
Also, the ability to be dismantled at the end of the building lifecycle should be considered. Under the motto “Screw it — don’t glue it,” all components should be separable from one another so that they can be economically dismantled and reused. These requirements apply not only for new buildings but also when demolishing or modernizing existing building stock.
At the Siemens Campus Erlangen, around 82,000 tons of material were generated during the demolition of old buildings. While constantly confronted with the challenge of nearly inseparable materials, the team was able to achieve high recycling and reuse rates. Around 80 percent of the demolition material could be recycled; even the floor panels of the raised floors were returned to the manufacturer for reuse and recycling. In the future, we will not only focus on the use of recycled products but also on the ability to dismantle construction products and materials by type.
Likewise, the new Siemens Campus in Zug — one of Siemens’ first climate-neutral locations — is another showcase for circular construction. Here, from the very beginning, our aim was to create a blueprint for sustainability. We also followed this philosophy when renovating the existing building. Our team examined several options for how the previously identified components could be reused in a circular manner. In one example, elements of the windows and the façade were used for the new construction of a nearby warehouse. This allowed transport routes to be kept short, landfill waste to be saved, and CO2 emissions to be minimized.
While new laws and regulations are promoting gradual change within the industry, at an international level no standard has yet been established. Without effective ecosystems in the supply and disposal chain and the corresponding expertise and know-how among planning and construction companies, the possibilities for implementing a circular building culture are still limited in many regions.
And yet, we can model forward. Circular construction means no longer simply consuming materials as before; it means extending their lifecycles in new forms and with new applications. Understanding this requires a fundamental rethink. While countries and industries move at different speeds, companies such as Siemens are well on our way and ready to help shape the future of the circular economy.
- SEO Powered Content & PR Distribution. Get Amplified Today.
- PlatoData.Network Vertical Generative Ai. Empower Yourself. Access Here.
- PlatoAiStream. Web3 Intelligence. Knowledge Amplified. Access Here.
- PlatoESG. Carbon, CleanTech, Energy, Environment, Solar, Waste Management. Access Here.
- PlatoHealth. Biotech and Clinical Trials Intelligence. Access Here.
- Source: https://www.greenbiz.com/article/transforming-buildings-circular-material-banks
- :has
- :is
- :not
- 000
- 1
- 2030
- 5
- 80
- a
- ability
- Able
- Achieve
- achieving
- Action
- aim
- All
- allowed
- almost
- also
- among
- amounts
- an
- and
- Annually
- Another
- apparent
- applications
- Apply
- approaches
- ARE
- around
- article
- AS
- At
- Banks
- BE
- been
- before
- Beginning
- Beyond
- blueprint
- Building
- Building Materials
- buildings
- but
- by
- Campus
- CAN
- chain
- challenge
- challenging
- change
- circles
- circular
- circular economy
- closed
- co2
- co2 emissions
- come
- Companies
- completely
- components
- concept
- considered
- constantly
- construction
- consuming
- continue
- conventional
- Corresponding
- could
- countries
- create
- Culture
- day
- dc
- decarbonization
- different
- disposal
- Dont
- economically
- economy
- Ecosystems
- Effective
- elements
- Emissions
- end
- environmental
- established
- estate
- estate industry
- Ether (ETH)
- Even
- Every
- everything
- example
- existing
- expected
- expertise
- extending
- façade
- familiar
- far
- First
- Floor
- floors
- Focus
- followed
- For
- forms
- Forward
- from
- fundamental
- future
- generated
- Global
- global investment
- gradual
- Grow
- help
- here
- High
- holistic
- How
- However
- HTML
- HTTPS
- huge
- idea
- identified
- immense
- implementing
- impressive
- in
- Increase
- industries
- industry
- integrated
- International
- into
- investment
- IT
- jpg
- kept
- Lack
- Laws
- Laws and regulations
- Level
- lifecycle
- lifecycles
- Limited
- linear
- locations
- longer
- Lot
- manner
- Manufacturer
- many
- material
- materials
- means
- model
- modernizing
- more
- most
- Motto
- move
- nearly
- needed
- New
- New Construction
- no
- now
- of
- Old
- on
- ONE
- only
- operation
- Opportunity
- Options
- or
- our
- panels
- paradigm
- particularly
- percent
- performance
- philosophy
- planning
- plato
- Plato Data Intelligence
- PlatoData
- Play
- possibilities
- previously
- producing
- Products
- professionals
- Progress
- promoting
- raised
- Rates
- Raw
- ready
- real
- real estate
- recycled
- recycling
- regions
- regulations
- regulations Are
- Requirements
- requires
- resource
- Resources
- reuse
- reused
- Role
- routes
- Save
- saved
- Scale
- sector
- several
- Shape
- shift
- Short
- should
- showcase
- Siemens
- significant
- simply
- So
- Sources
- speeds
- Sponsored
- standard
- Still
- stock
- such
- supply
- Sustainability
- taking
- targets
- team
- that
- The
- The Future
- their
- There.
- These
- they
- Thinking
- this
- to
- tons
- transforming
- transition
- transport
- Trillion
- Turned
- type
- typically
- under
- understanding
- until
- use
- used
- Valuable
- very
- View
- Warehouse
- was
- Waste
- Way..
- we
- WELL
- were
- when
- which
- while
- will
- windows
- with
- within
- without
- world
- yet
- zephyrnet